Cyclone
Cyclone is a 23’ trimaran, “foldable” to allow her to be transported over the road. Designed by the talented John Marples, she was built using the “Constant Camber” method developed by John and Jim Brown. It’s similar to stitch-and-glue but instead of using sheet plywood, one creates their own compound-curved panels and joins them together to create the hulls; ingenious and very effective. She was an ambitious project for us, not made any easier by my elaborations including cambered decks over laminated fir deckbeams, a teak-strip cockpit sole, 2-part LPU paint, and an asymetrical spinnaker set on a retractable bowsprit. No Hobie Cats were harmed in the building of this Cyclone; custom rigging was by Manta Marine and sails by Dave Bierig.
Freed from any pretense of trying to cram a cabin into a 23’ boat, Cyclone is a beautifully performing, spacious daysailing trimaran with what I find to be graceful and elegant lines…..call me blasphemous, but I have always thought of her as the mutihull equivalent of Rozinante. She spent the first 15 years sailing the Columbia River. After being trailered cross-country behind my old Volvo wagon, she spent the next 15 years exploring the New England coastline from her home port of Salem. Recently she moved on to a new owner and is now sailing the Chesapeake.
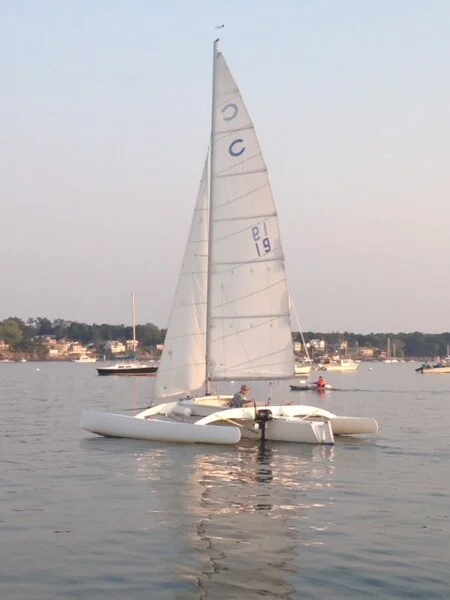
Cyclone in light air in her homeport of Salem Harbor
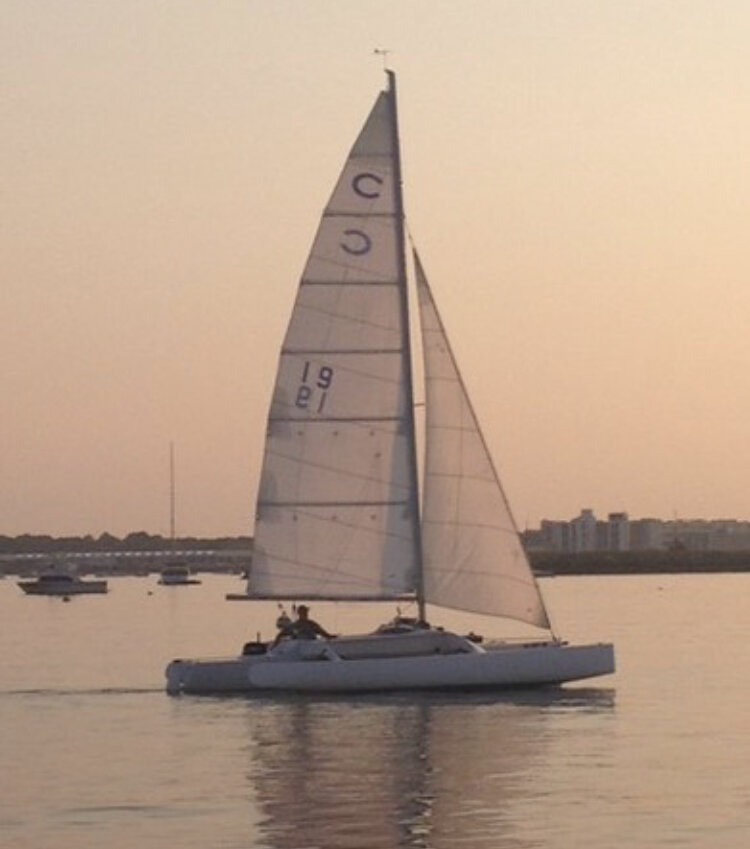
Returning home at dusk
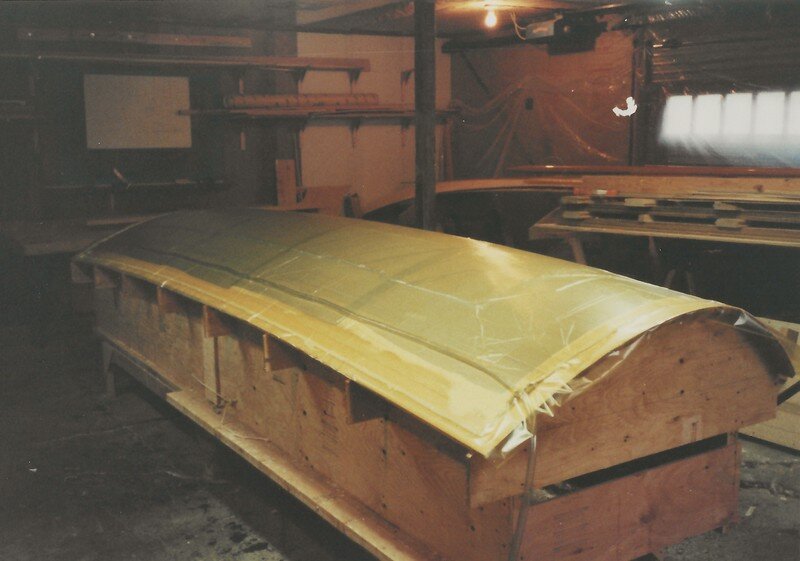
Layup of a hull panel underway. Panels were constructed from outer veneers of 1/16" clear fir, with inner layers of 1/8" western red cedar (2 inner core layers for the main hull, one for the outer hulls or "amas").
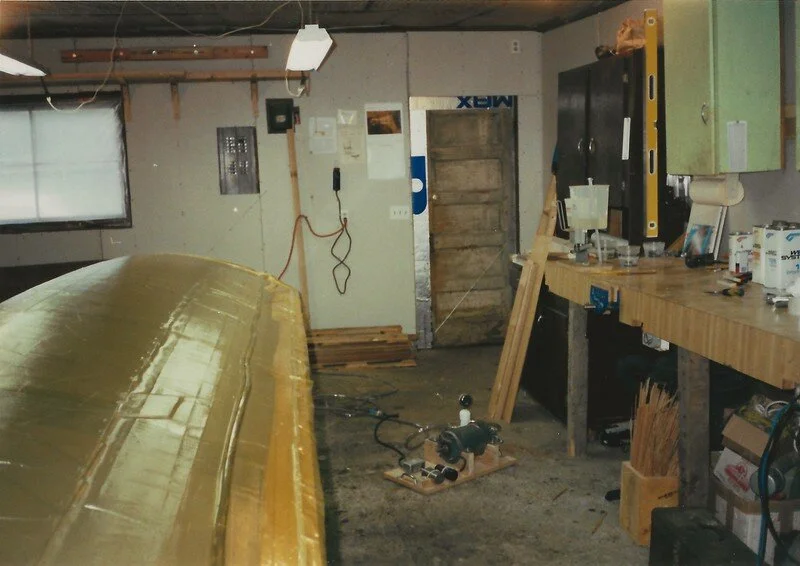
Staple the veneers around the edges to hold them in place until the vacuum bag can be affixed, get the pump running, and then you've earned a beer. Repeat 12 times and you have all the panels needed for Cyclone.

A completed panel ready for cleanup. An outer layer of fiberglass was applied while the panels were still on the mold.
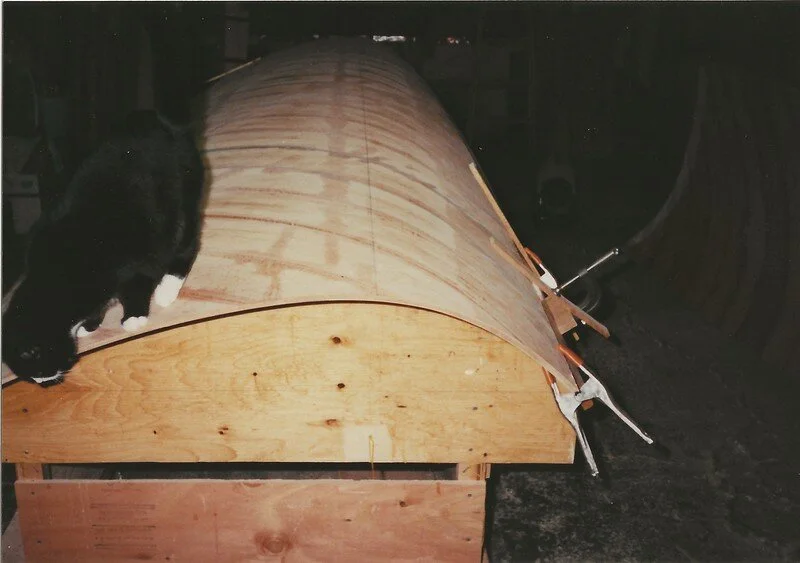
No panels were released into production without a thorough QC inspection.
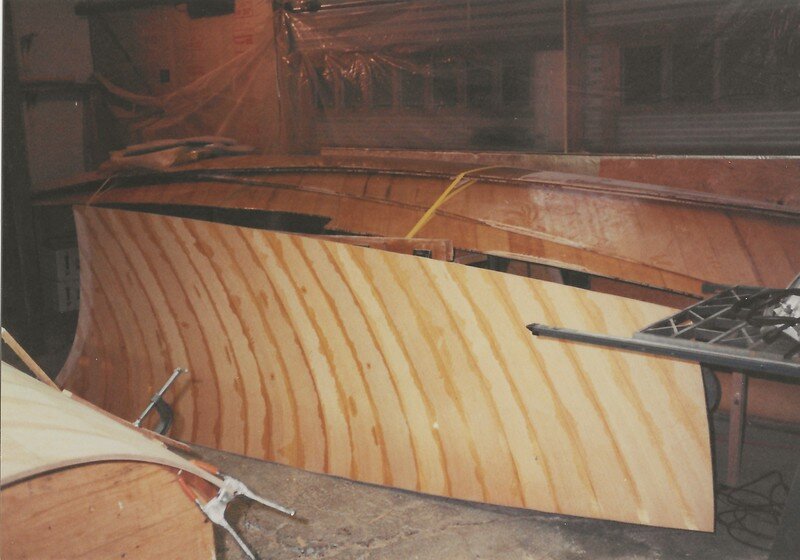
Completed panels stacked and awaiting assembly.
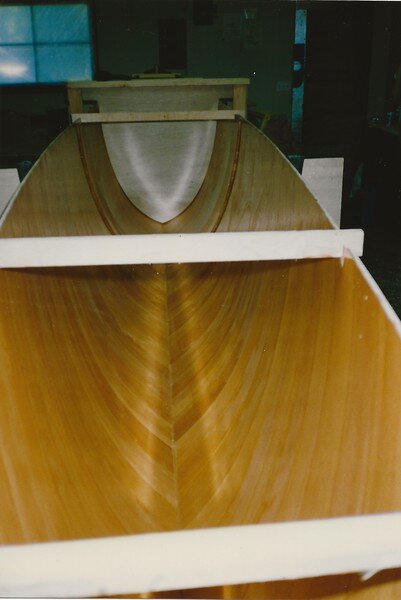
The completed half-length panels were joined with butt blocks and wired together along the keel. The outside of the joint was reinforced with biaxial tape and the interior will be reinforced with fillets.

Assembled outer hulls ("amas") being repositioned to make room in the shop to assemble the main hull.
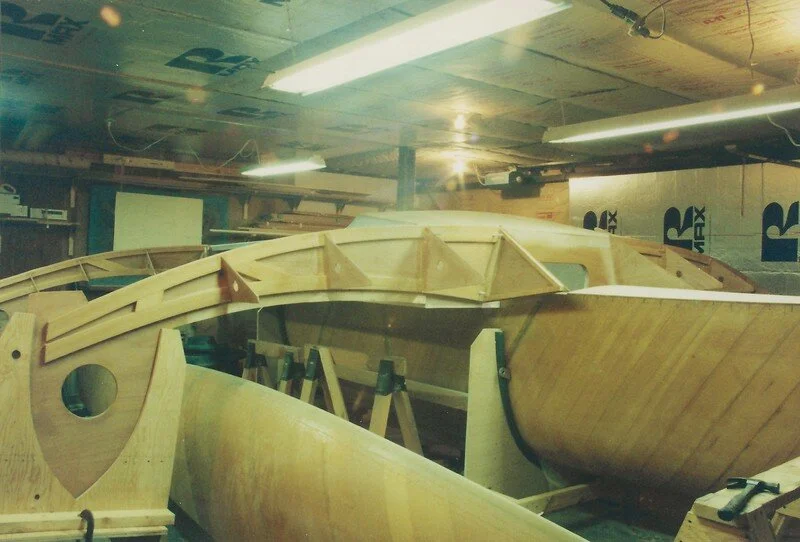
Framing the crossarms ("akas") in preparation for bonding them to the amas.

Amas bonded to the akas. Everything needed to be carefully measured and aligned to close tolerances to ensure that the folding mechanism would work smoothly.

Amas attached and decking being bonded over laminated frames.

Amas and akas taped around the edges and faired for primer.


Centerboard trunk installed and cockpit sole framed.

Looking aft from the front cuddy into the cockpit; the bulkheads will later be filleted to the hull. The stainless steel supports for the folding mechanism have been attached to the bulkhead.

Looking forward from the stern; coaming for the aft hatch installed and ready for decking.
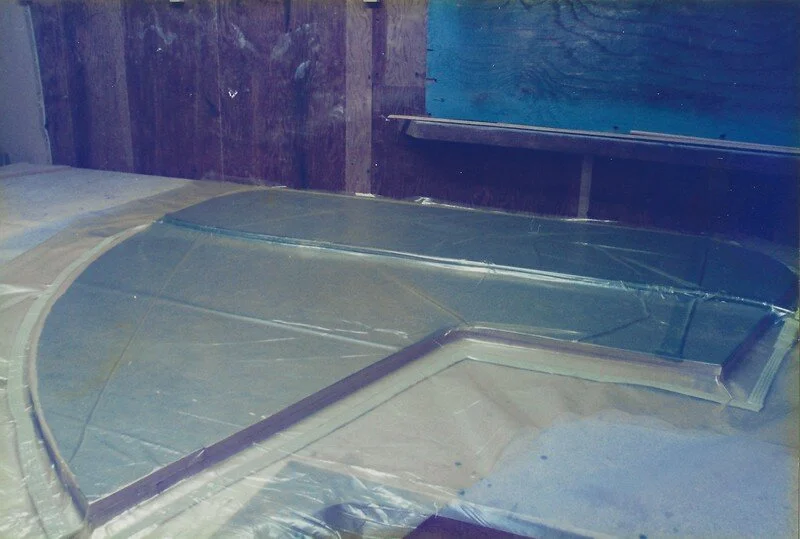
Vacuum-bagging the plywood core of the centerboard.
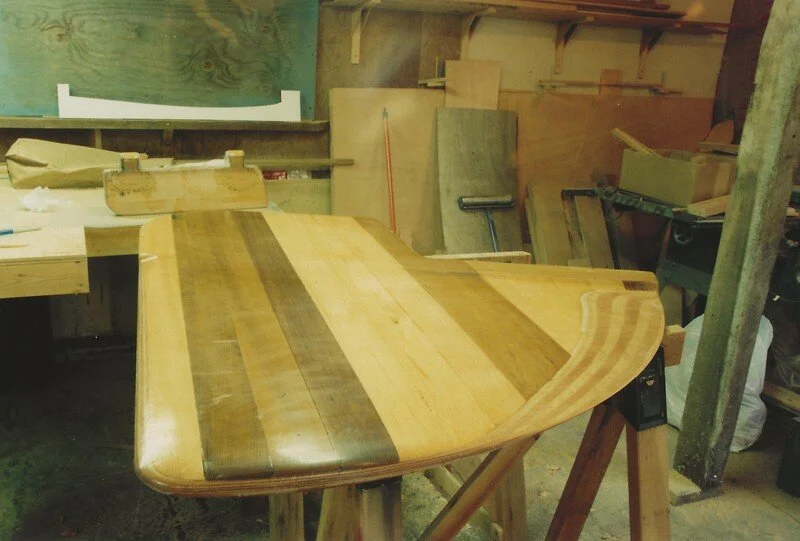
Centerboard built up to thickness, shaped and ready for fiberglass covering.
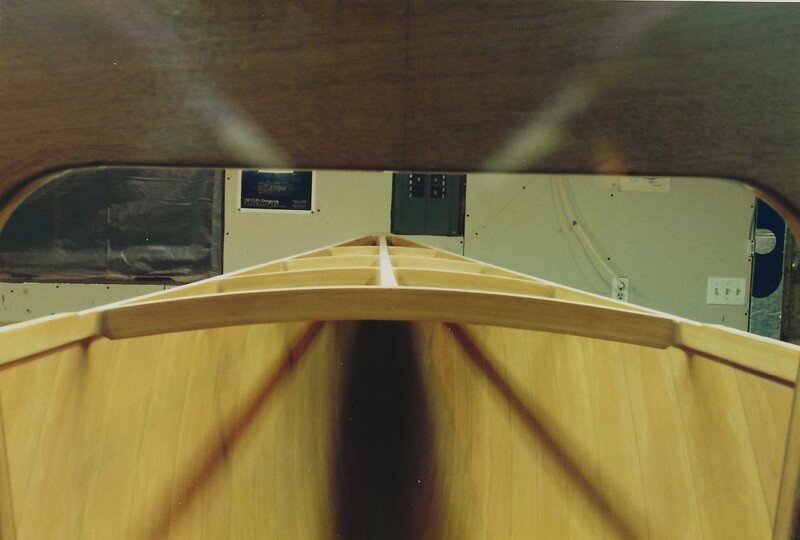
Forward deckbeams ready for decking.
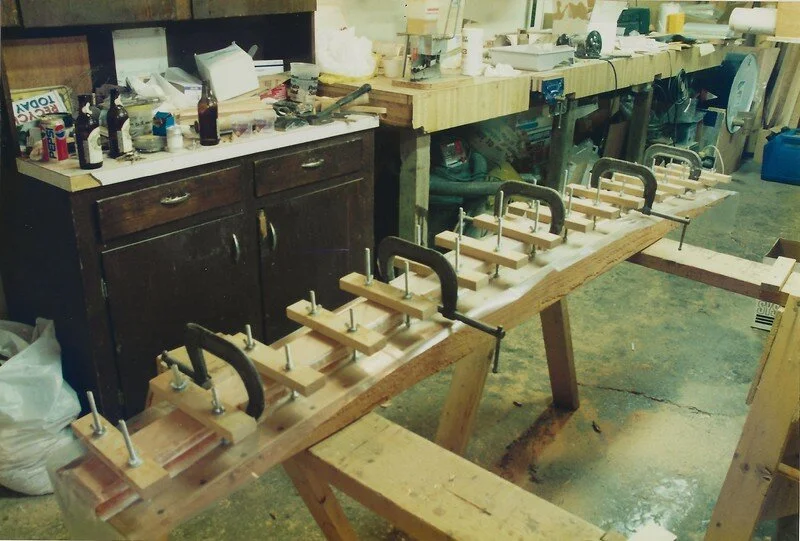
Laminated beam to support the cuddy roof. Yes that is a 55-gal drum of WEST epoxy in the background..... and it still wasn't enough to finish the project.
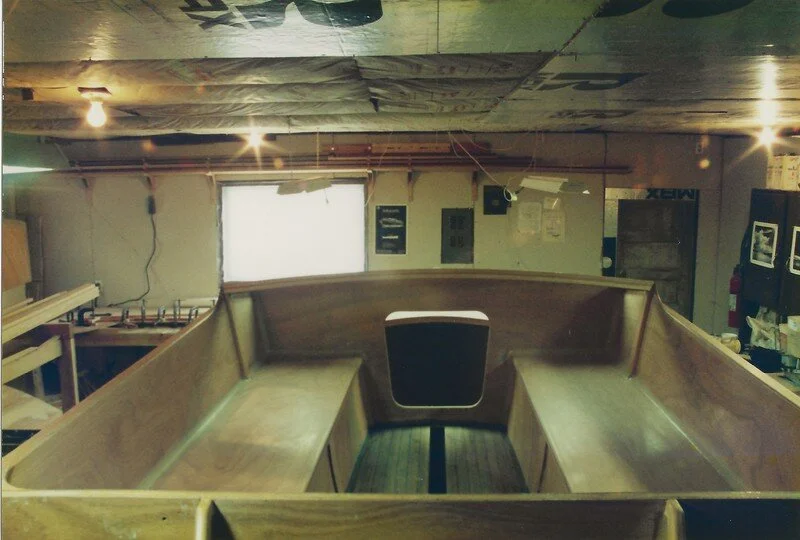
Looking forward into the cuddy; the cockpit seats are a full 8' long. Teak-strip cockpit sole has been installed.

Early sea trials on the Columbia River.
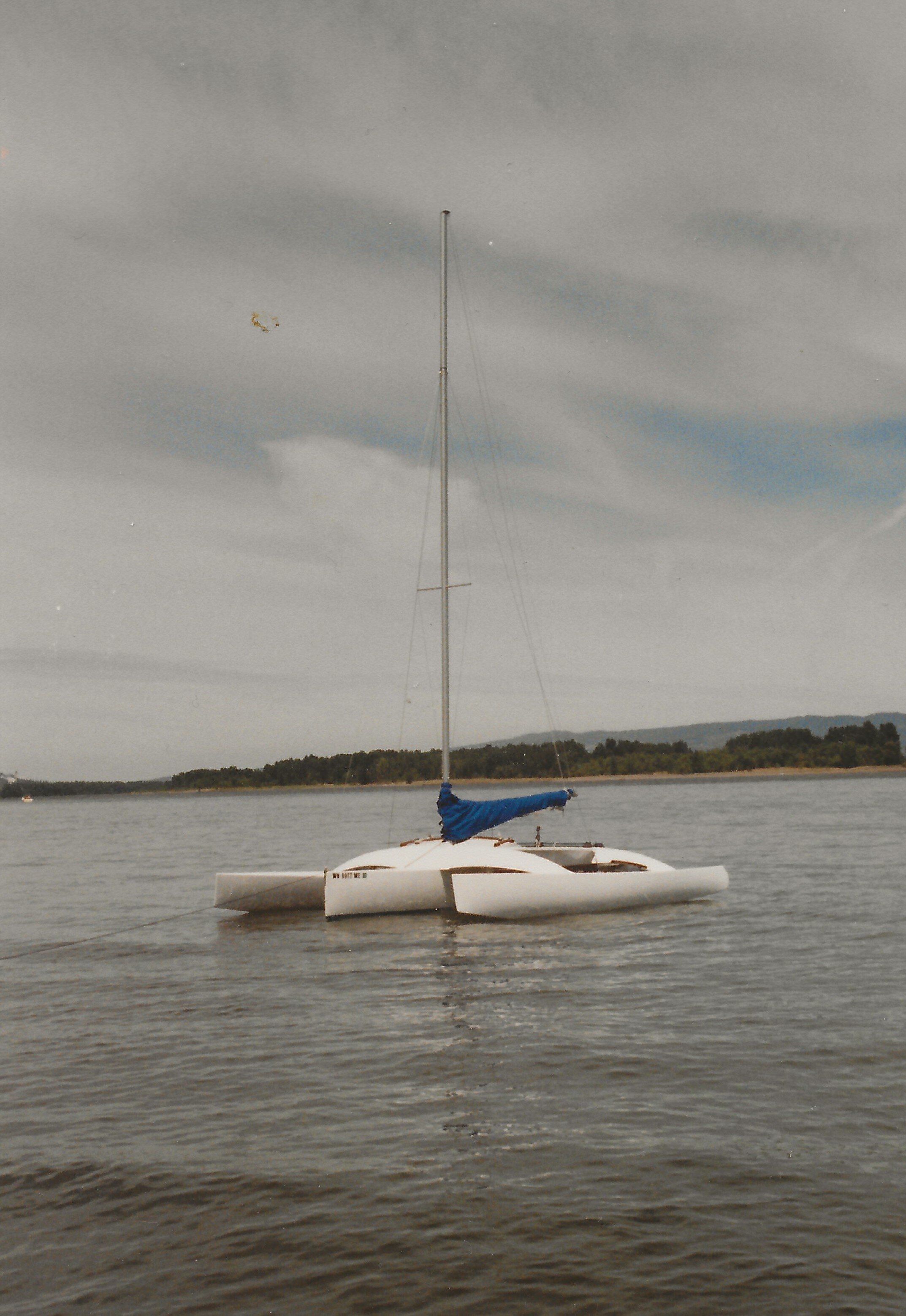
Sauvie Island on the Columbia River.
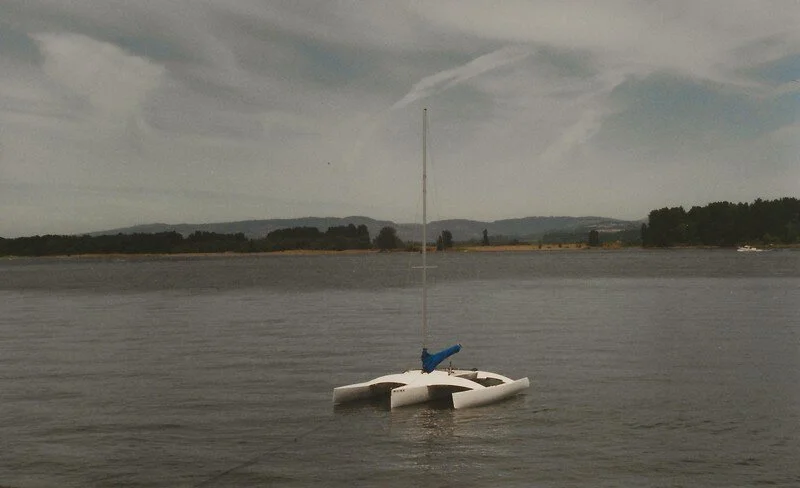
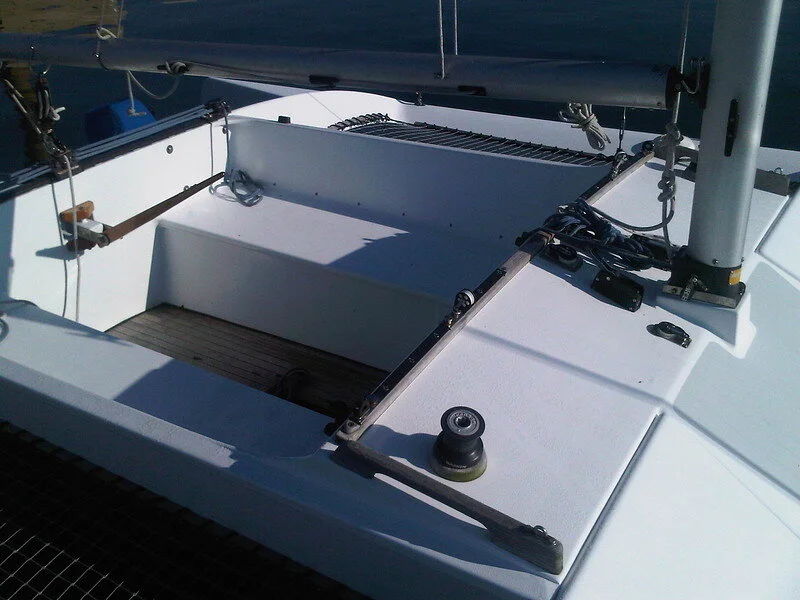
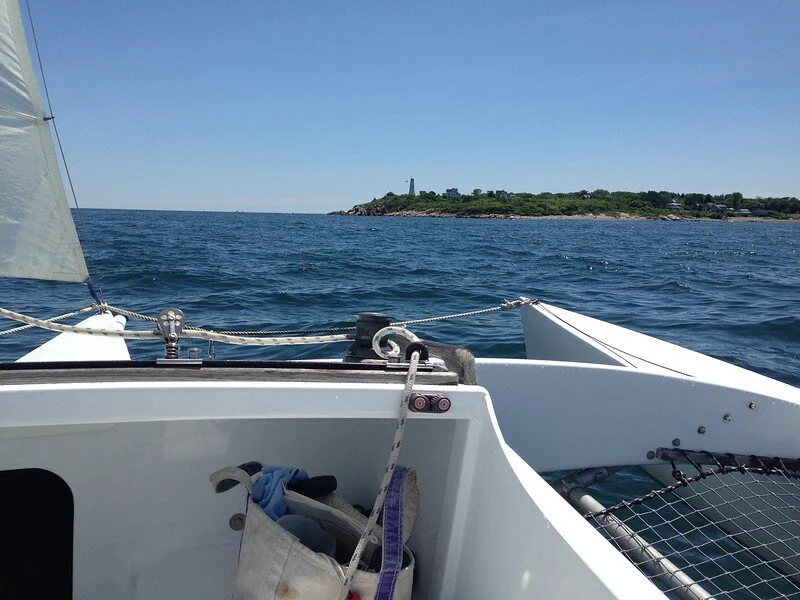
A daysail from Salem out around the Baker's Island Light.

Interior support for the retractable bowsprit.

Exterior of the retractable bowsprit.

Moored at Salem Harbor.
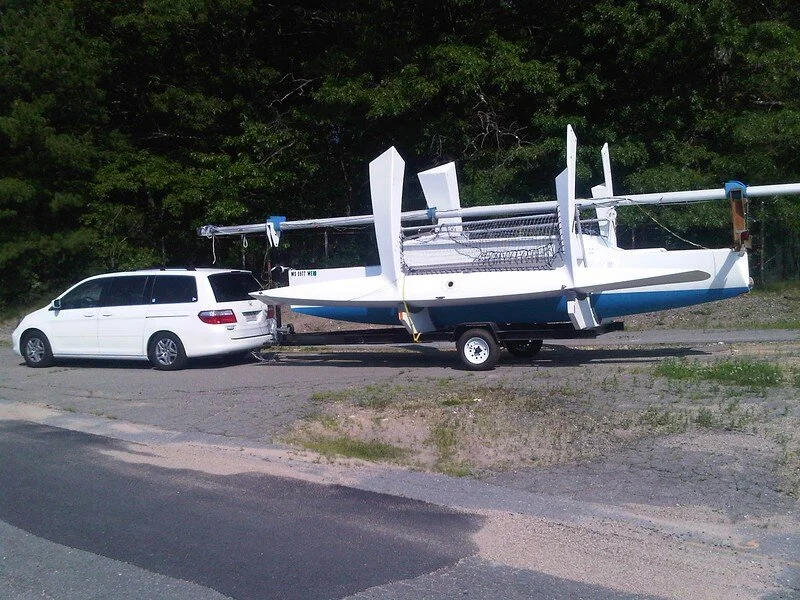
Folded for transport

Thank you Olie for the painting!